CAMを用いてSTLデータからNCコードを生成しCNCフライスで加工するときに思ったことをつらつらと書きます。
CADCAMについて、何か専門的に勉強したことがあったり、何らかの科目で説明を受けたりということは一切ないので、ネーットサーフィンと実際にやってみた!事実をもとに考えてみたことなので、ある意味常識てきなこと、あるいは非常識なことを多分に含んでいるし、内容が他大多数の人と共有できる物なのかどうかということには
全く興味が無いですが、自分の備忘録としてまとめたものです。
機材:
miniCNC-HAKU MACH3
エンドミルはミスミの10DロングエンドミルΦ2
切り込み量0,2mm
x-y送り600mm/min
z送り100mm/min
主軸(設定上8000rpm)
CAMソフト:
Cut3D(http://www.originalmind.co.jp/goods/03518)
MeshCAM(http://www.originalmind.co.jp/goods/03516)
アジェンダ
■Cut3Dで部品がガタガタに削れた!
■STLの解像度って何だ?
■解像度を変えて加工してみる!
■MeshCAMってなに?
■切削時間とNCコード生成とやる気
◇そもそも
こんな感じの部品
材質ABS
高さ10mm
150x150ぐらいのサイズ。
与えられている材料
厚み10.8mmの板
やりたい加工
0.8mm表面を削る
2次元パスを削る
◇結論
Cut3Dは微妙。MeshCAMはまーゆるせる。
◇ガタガタ
今回削ったものを右から順に並べます。
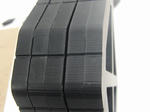
右から①②③④⑤の加工とします。
まず①を加工しました。
斜めのところ、Rのところがガタガタです。
は?と思います。
軸がぶれぶれとか、メカ的なバックラッシュとか・・・かな?
と思いました。
ですが、②の時は加工の一部始終を見ていましたがそんな感じはしないし、
実際にメカをオラオラってゆすってみてもバックラッシュはないかな?
少なくともこんなにガタガタは感じないし。
そもそも斜めの面に出てる時点でx-y軸いずれもバックラッシュがあると仮定すると、
他のまっすぐパスのx移動からy移動に変わった時に後ができるハズだし・・・
(これって円が削れないよね…)
ソフトてきな?はいはい、では加工の流れでソフトが絡む部分を考えます。
3DCAD作る⇒STLで保存⇒CAMソフトで読み込み⇒切削パラメータ入れて⇒NCコード生成
少しネットサーフィンして、STLが有限要素法みたいに3角形にするものだと知った。
つまり?細かい直線がいっぱいで曲線を表すっぽい。
へ?曲線斜めって直線だし…。
は?は?
じゃあ、NCパスを眺めてみるか
NCviewerなるものをグーグル先生に教えてもらい
つかう。
横の平行ラインは0.8mmの削りです。←まーどーでもいい。
問題は横線とRと斜め線の部分。
よーく見るとガタガタである。
つまりNCコードはガタガタ、メカは正常に動いている!!敵は何処や?
Cut3Dのパラメータとか?
STLデータの解像度とか?
Cut3Dの設定をなめまわす。
それっぽい設定はなんにもない。
じゃあSTLの解像度的な?
STLの保存の際の設定を見る。
おっと割といろんな設定があった←しらなかった…。
これかも!!(ぬかよろ。)
で、設定をいろいろ変えてみた。
で上の②③④の加工順に解像度を上げたわけです。
写真をみるとおり、みんなガタガタ、ガタガタの様子が少し筒違いますが・・・
まー、振幅の大きさは変わらないというか・・・
STLの解像度ではなかった!
CADの寸法精度的なそんなバナナ。(Cut3D以前に2DのCAMでは何べんもやってみて問題なかった経験大アリ)
では
Cut3Dの設定or仕様そこで来たのが、別の3DCAMを使ってみる。
辛辣な後輩から提案されたのはMeshCAM...
説明を読むと製作元が違う
・安い
・仕上げパスの種類が多い
・フリーフォー15日
ふむふむやってみる。
試行錯誤の後同じような部品が作れると思われるパスを生成。
Cut3Dとはチト趣が違う。簡単に言えば
◇Cut3D⇒2種一括パス(0.8までジオメトリの形状オフセット刃径含む、に表面を削る)+(ジオメトリの形状に合わせ一番下まで、0.2ずつ等高パス)
◇MeshCAM⇒2種別パス・・・設定を変えて2度パスを生成する。
1、表面を削る…これが難しい。ジオメトリ形状まではできる、問題は刃径オフセット付けると10.8まで削ろうとする。表面だけじゃなくて溝に手を出し始める。
2、等高パス…これはちょっと難しい。材料設定を10.8にしても、部品が10mmだと野郎は(仕上げパスだし…)と思っているのか10mmから削り始める。
※気付いたかもしれないが、オフセット無しの表面削りと、10mmからの等高パスを連続でやると…等高パスはジオメトリ形状の外側をエンドミルが通るわけで・・・一回めの切り込みが10.8ある部品に0.8以上一気に切り込むことになります。
まー樹脂ならいいかもですが、アルミとかはとても無理かと思います。
実際は刃径の7割ぐらいオフセットして表面削りパスを作ることで緩和できますが…緩和しかできません。
俺は気付いた!!
表面削りの時の材料の厚みを0.8しかないことにすればよくね!!10mmからしかジオメトリが無いので、ジオメトリ形状が選べません…
なので0.8+一回分の切り込み量ぐらいの材料サイズにするのが正解か?
というわけで
写真一番左の綺麗な面の加工が完了しました。
一個目の加工が終わってから、もう一回データ入力して2個目の加工ってなるので手間ですね。
◇この手間を持ってすれば、削れます。一発でやりたい人はガタガタに成るでしょう…。
俺は1発でやりたかったんですが…
今のところムリです。
おわり
[5回]